Proximity to Transportation Routes
Access to Essential Utilities
As part of Rwanda’s broader industrialization strategy, the Bugesera Special Economic Zone is a public-private partnership aimed at transforming the district into a regional manufacturing powerhouse. The ongoing infrastructure upgrades and focus on key sectors like agro-processing and construction materials make it a future-ready location for investment.
The district is committed to workforce development, with local training initiatives tailored to industrial needs. This ensures access to a growing pool of skilled labour essential for refinery operations.
Raw beryllium ore, containing 8.80% beryllium oxide and 3.09% pure beryllium, is transported to the facility. Each batch undergoes initial inspection to ensure quality standards are met before entering the production line. Proper handling during this stage minimizes loss and contamination.
The facility is designed to process 50 tons of ore per month under a two-shift operation. To ensure uninterrupted operations, 300 tons of ore will be stockpiled in advance, guaranteeing six months of production. This raw material is secured through supplier agreements and supplemented by the project’s own mining operations, which will sustain future production cycles. The refinery will maintain a consistent stockpile of 250-300 tons to avoid disruptions.

The ore is crushed into smaller fragments and milled to achieve a fine powder with a particle size of less than 0.074 mm. This increases the ore’s surface area, optimizing it for chemical reactions in subsequent stages. Spiral classifiers separate oversized particles, recycling them back for additional milling.

The milled ore is mixed with carefully measured reagents to enhance its reactivity during extraction. The mixture is then compressed into briquettes using advanced briquetting equipment. These briquettes are heated in a tunnel kiln to activate the reagents and improve the material’s chemical properties.
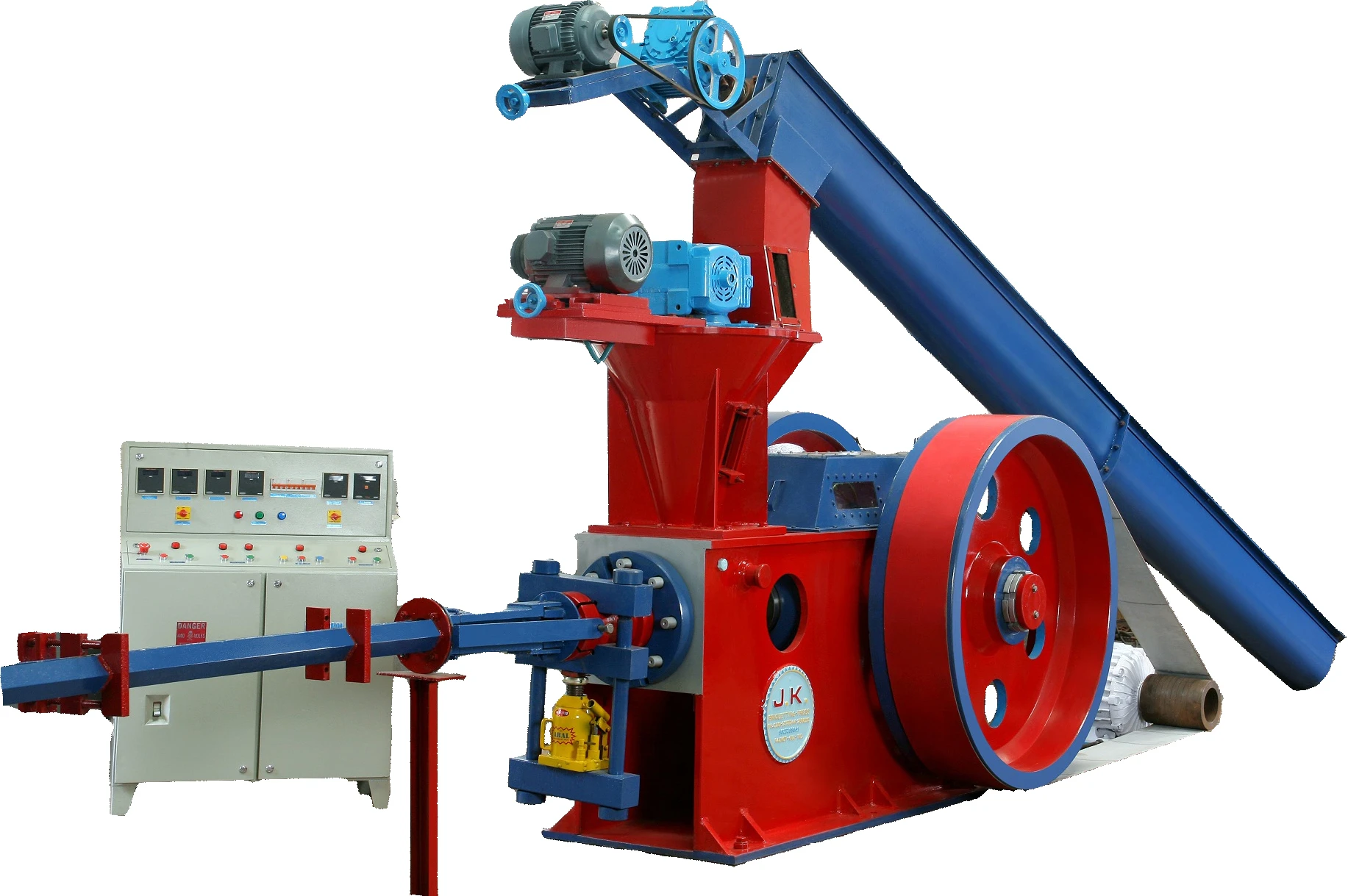
Heated briquettes are subjected to chemical washing and agitation in a multi-stage extraction process. This phase ensures that beryllium hydroxide [Be(OH)2] is efficiently separated from other components. Waste products are carefully managed to minimize environmental impact.

The extracted beryllium hydroxide is fed into a high-temperature rotary kiln, where it is refined into industrial-grade beryllium oxide with over 99% purity. The process is meticulously controlled to ensure consistent quality and minimize energy usage.

The refined beryllium oxide is cooled and packaged securely to preserve its quality during transportation. Packages are labelled according to international standards and prepared for shipment to domestic and international clients.

Establishing the business, taking advantage of the profitable processing of beryllium, and solidifying its position within the global beryllium marketplace. The project aims to maximize profitability while expanding its influence in the international market, ensuring long-term growth and competitiveness.
The project provides employment opportunities, supports skills development, and enhances infrastructure, including roads, electricity, water systems, and other essential services. It employs 18 workers operating in two shifts, ensuring consistent productivity and stable income for the workforce. These combined efforts contribute to both individual and community growth.